In the competitive landscape of compressor solutions across the US, HPDMC stands out with a robust offline service network designed to deliver lightning - fast after - sales support.
Spanning from the sun - drenched streets of Los Angeles to the bustling industrial hubs of Chicago, our offline stores, anchored by three strategically located warehouse pick - up points (968 W Foothill Blvd, Azusa, CA 91702; 1247 Naperville Dr, Romeoville, IL 60446; 1135 W Elizabeth Ave, Linden, NJ 07036), redefine compressor repair and maintenance efficiency.
Here’s how we make “30 - Minute Express Response” a reality for businesses relying on our compressors.
1. Spare Parts Inventory System: The Backbone of Swift Repairs
At HPDMC, we understand that every minute of compressor downtime costs our customers money. That’s why our offline stores maintain a comprehensive spare parts inventory tailored to the most common repair needs of our compressors.
- Strategic Stocking: Each of our three US warehouse pick - up points is stocked with high - demand components like rotors, bearings, seals, and filters for our entire range of compressors—from small commercial models to heavy - duty industrial units. For example, our Azusa, CA location keeps a large inventory of parts for the Portable Gasoline Power Piston Air Compressor 6.5HP, a favorite among local contractors.
- Real - Time Inventory Sync: Our inventory management system is synced across all offline stores and online platforms. When a customer contacts our service team, we can instantly check the availability of required parts at the nearest warehouse. This eliminates the delay of waiting for parts to be shipped from distant locations, slashing repair timelines.
By ensuring that critical spare parts are within easy reach, we set the stage for rapid repairs—often getting the necessary components in the hands of our engineers within 30 minutes of a service request.
2. Engineer Training Mechanism: Experts Ready to Respond
A well - stocked parts inventory is only as good as the team that uses it. HPDMC invests heavily in engineer training to create a workforce capable of delivering fast and effective repairs.
- Specialized Compressor Training: Our engineers undergo rigorous training programs focused on HPDMC compressor technology. They learn the intricacies of our product line, from the core components of our screw compressors to the unique features of our portable models. This deep product knowledge allows them to diagnose issues quickly and accurately.
- On - Site Simulation Training: We conduct regular on - site simulation exercises at our offline stores, replicating common compressor breakdown scenarios. Engineers practice troubleshooting, part replacement, and system testing under timed conditions, honing their ability to deliver the “30 - Minute Express Response” in real - world situations.
- Continuous Skill Upgradation: As we introduce new compressor models and technologies, our engineers participate in ongoing training sessions. This ensures they stay up - to - date with the latest repair techniques and can handle even the most advanced HPDMC compressors with confidence.
With a team of highly trained engineers at each offline store, we’re equipped to tackle compressor issues head - on, minimizing downtime for our customers.
3. 24 - Hour After - Sales Hotline: Always Available
Compressor problems don’t adhere to a 9 - to - 5 schedule—so neither does our support. Our 24 - hour after - sales hotline serves as the first point of contact for customers facing compressor emergencies.
- Rapid Triage: When a customer calls our hotline, our trained customer service representatives perform a quick triage. They gather information about the compressor model, the nature of the problem, and the customer’s location. Using this data, they can immediately determine if the issue can be resolved remotely (e.g., via troubleshooting guidance) or if an on - site visit from an engineer is required.
- Dispatch to Nearest Store: If an on - site visit is needed, the hotline team dispatches an engineer from the nearest HPDMC offline store or warehouse pick - up point. Thanks to our strategic locations, this means an engineer can often reach the customer’s site quickly—sometimes within 30 minutes in urban areas—to start the repair process.
This round - the - clock availability ensures that our customers never have to wait long for help, no matter when a compressor issue arises.
Customer Proof: Testimonials of Exceptional Service
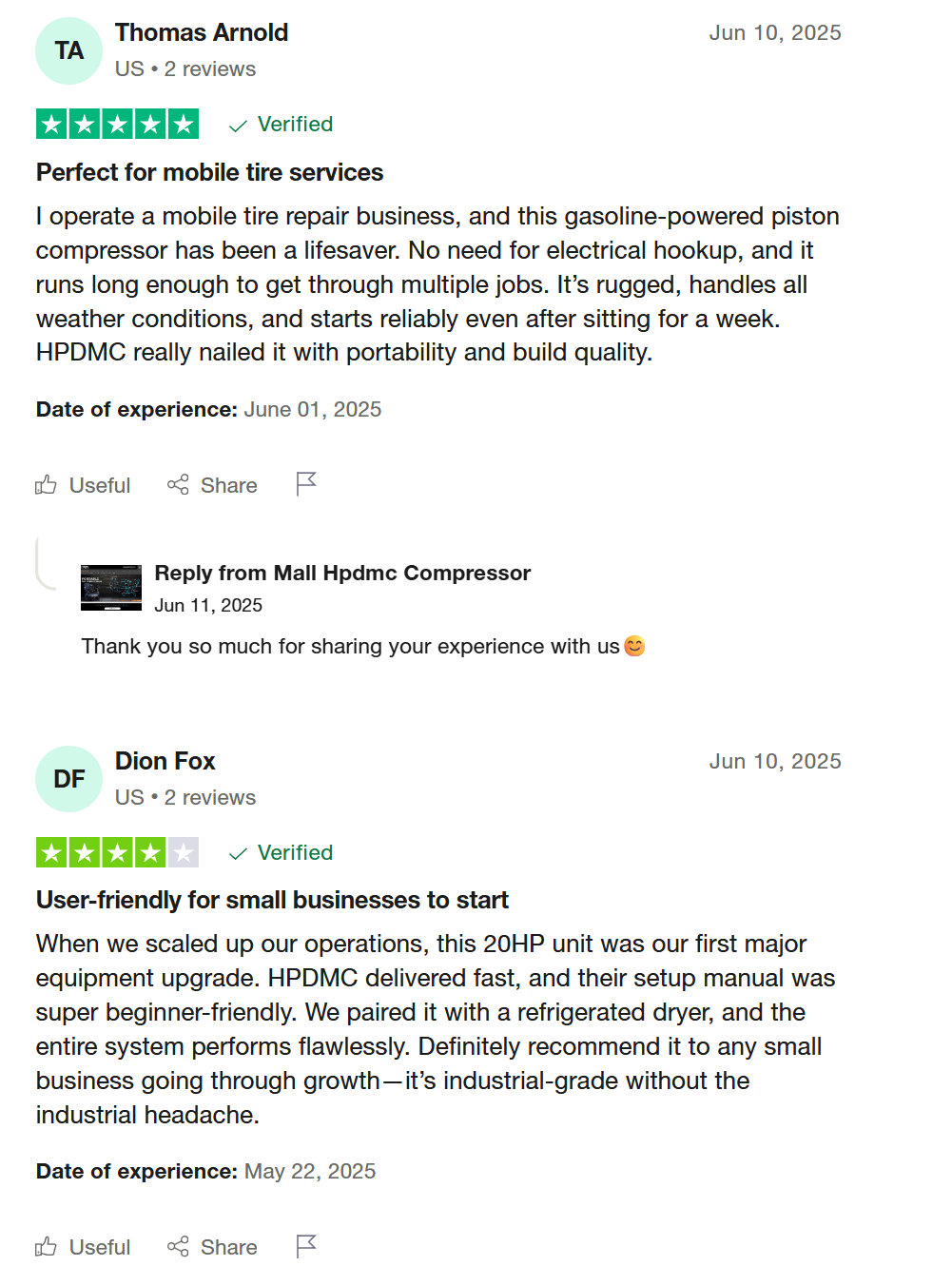
Experience the HPDMC Difference
Whether you’re in California, Illinois, New Jersey, or anywhere across the US, HPDMC’s offline stores are committed to keeping your compressors running smoothly. With a powerful combination of a well - stocked spare parts inventory, highly trained engineers, and a 24 - hour hotline, we’ve set a new standard for after - sales service in the compressor industry.
To learn more about our products and services, or to experience our “30 - Minute Express Response” firsthand, visit our online mall or reach out to your nearest HPDMC offline store:
- California: 968 W Foothill Blvd, Azusa, CA 91702
- Illinois: 1247 Naperville Dr, Romeoville, IL 60446
- New Jersey: 1135 W Elizabeth Ave, Linden, NJ 07036
Trust HPDMC to keep your operations running—fast, efficient, and always ready to respond.